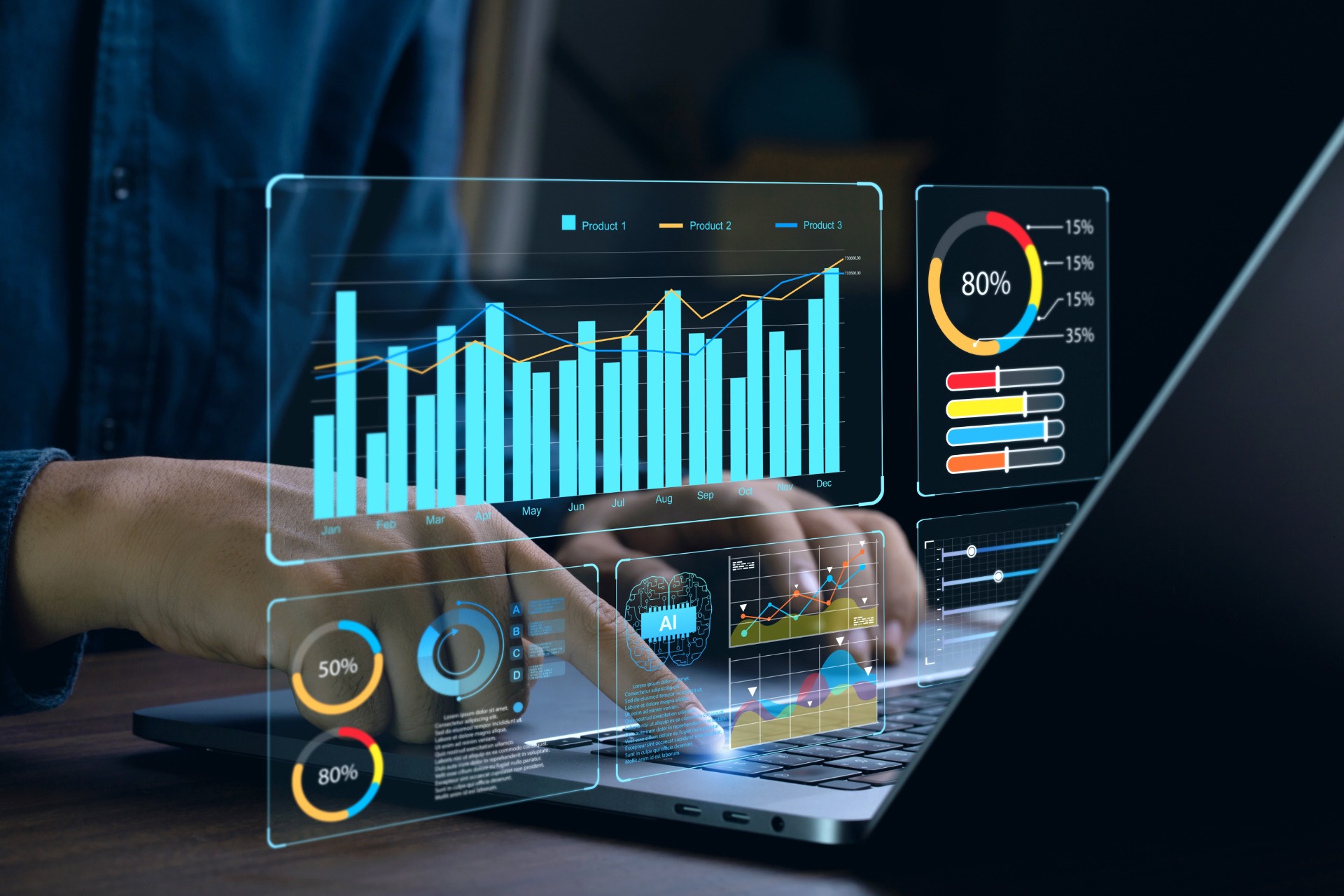
LEAN
"Lean" is a term that can have various meanings depending on the context in which it's used. Here are a few common interpretations:
Lean Manufacturing: This is a production philosophy that focuses on maximizing value while minimizing waste. Originating from the Toyota Production System (TPS), lean manufacturing aims to streamline processes, reduce costs, and improve efficiency by eliminating activities that don't add value to the final product or service.
Lean Management: Beyond manufacturing, lean principles have been applied to various other industries and sectors, including services, healthcare, and software development. Lean management involves organizing processes and teams to continuously improve efficiency, quality, and customer satisfaction.
Lean Startup: In the entrepreneurial realm, a "lean startup" refers to a methodology for developing businesses and products based on validated learning, experimentation, and iterative product releases. The core idea is to build a minimum viable product (MVP) to quickly test assumptions and gather feedback from customers, then iterate and pivot based on that feedback.
Lean Six Sigma: Combining principles from lean manufacturing and Six Sigma, this methodology aims to improve business processes by identifying and eliminating defects, errors, or inefficiencies. It focuses on achieving near-perfect quality by reducing variability and waste.
Lean Thinking: This encompasses the broader mindset and principles behind lean methodologies, emphasizing continuous improvement, respect for people, and delivering value to customers. It encourages organizations to question existing practices and relentlessly pursue efficiency and effectiveness.
In essence, "lean" in various contexts promotes efficiency, waste reduction, and continuous improvement to achieve better outcomes.
"Muda," "Mura," "Muri," and "Genchi Genbutsu" are key concepts in Lean manufacturing and management philosophy, primarily associated with Toyota's production system. Each term represents a different type of waste, challenge, or principle that organizations strive to identify, eliminate, or address to improve efficiency, quality, and effectiveness. Here's a brief explanation of each:
Muda: Muda refers to waste, or any activity that consumes resources without adding value to the final product or service. There are seven types of muda commonly identified in Lean thinking:
- Overproduction: Producing more than what is needed or demanded.
- Waiting: Idle time spent waiting for resources, materials, or information.
- Transportation: Unnecessary movement or transportation of materials or goods.
- Inventory: Excess inventory beyond what is required for immediate use.
- Motion: Unnecessary movement or motion of people, equipment, or materials.
- Overprocessing: Performing unnecessary or redundant processing steps.
- Defects: Errors, mistakes, or defects that require rework or correction.
Mura: Mura refers to unevenness or variability in the production process. It can lead to inefficiencies, bottlenecks, and disruptions in workflow. Mura can manifest as fluctuations in demand, uneven workloads, or imbalances in resource utilization. Lean aims to reduce mura by creating standardized processes, leveling production, and smoothing workflow to achieve greater stability and consistency.
Muri: Muri refers to overburden or strain on people, equipment, or systems. It occurs when tasks or processes exceed their capacity or capability, leading to stress, fatigue, errors, and reduced performance. Muri can result from factors such as excessive workloads, unrealistic expectations, or inadequate resources. Lean seeks to eliminate muri by optimizing workloads, balancing tasks, and improving resource allocation to create a sustainable and healthy work environment.
Genchi Genbutsu: Genchi Genbutsu, often translated as "go and see for yourself," emphasizes the importance of first hand observation and direct engagement with the actual work environment and processes. It encourages managers and decision-makers to go to the gemba (the place where work is done) to gain insights, gather information, and understand root causes of problems. By observing operations firsthand, leaders can identify opportunities for improvement, make informed decisions, and foster a culture of continuous learning and improvement.
Together, these concepts form the foundation of Lean thinking and provide a framework for identifying and addressing waste, variability, overburden, and the importance of direct observation in achieving operational excellence and continuous improvement.
In the context of Agile methodologies, "Lean" typically refers to the integration of Lean principles with Agile practices to enhance efficiency, reduce waste, and improve overall effectiveness in software development and project management. Here's how Lean principles are often incorporated into Agile
Value Stream Mapping: Lean emphasizes understanding the entire value stream of a process, from ideation to delivery. In Agile, teams may use techniques such as value stream mapping to identify and eliminate non-value-added activities or bottlenecks in their development processes.
Minimizing Waste: Lean principles identify various forms of waste, such as overproduction, waiting, unnecessary transportation, defects, and over-processing. Agile teams aim to minimize waste by focusing on delivering only what's necessary, avoiding unnecessary handoffs, and continuously improving their processes.
Kaizen (Continuous Improvement): Lean encourages a culture of continuous improvement. Similarly, Agile methodologies promote regular retrospectives where teams reflect on their work and identify opportunities for improvement. By adopting a mindset of kaizen, teams can iteratively enhance their processes and deliver greater value.
Pull Systems: Lean promotes the use of pull systems, where work is pulled based on customer demand rather than pushed based on predefined schedules. Agile frameworks like Kanban apply pull principles by limiting work in progress (WIP) and allowing teams to pull new work only when capacity becomes available.
Respect for People: Lean emphasizes respecting and empowering people at all levels of the organization. Agile methodologies prioritize self-organizing teams and emphasize collaboration between stakeholders, fostering an environment where individuals are empowered to make decisions and contribute to the success of the project.
Optimizing Flow: Lean focuses on optimizing the flow of work through the value stream to minimize delays and maximize efficiency. Agile practices such as continuous delivery, small batch sizes, and iterative development help teams achieve smoother and more predictable flow, enabling faster feedback and adaptation.
By integrating Lean principles with Agile practices, teams can create a more responsive, efficient, and customer-focused approach to software development, ultimately delivering greater value to their customers.
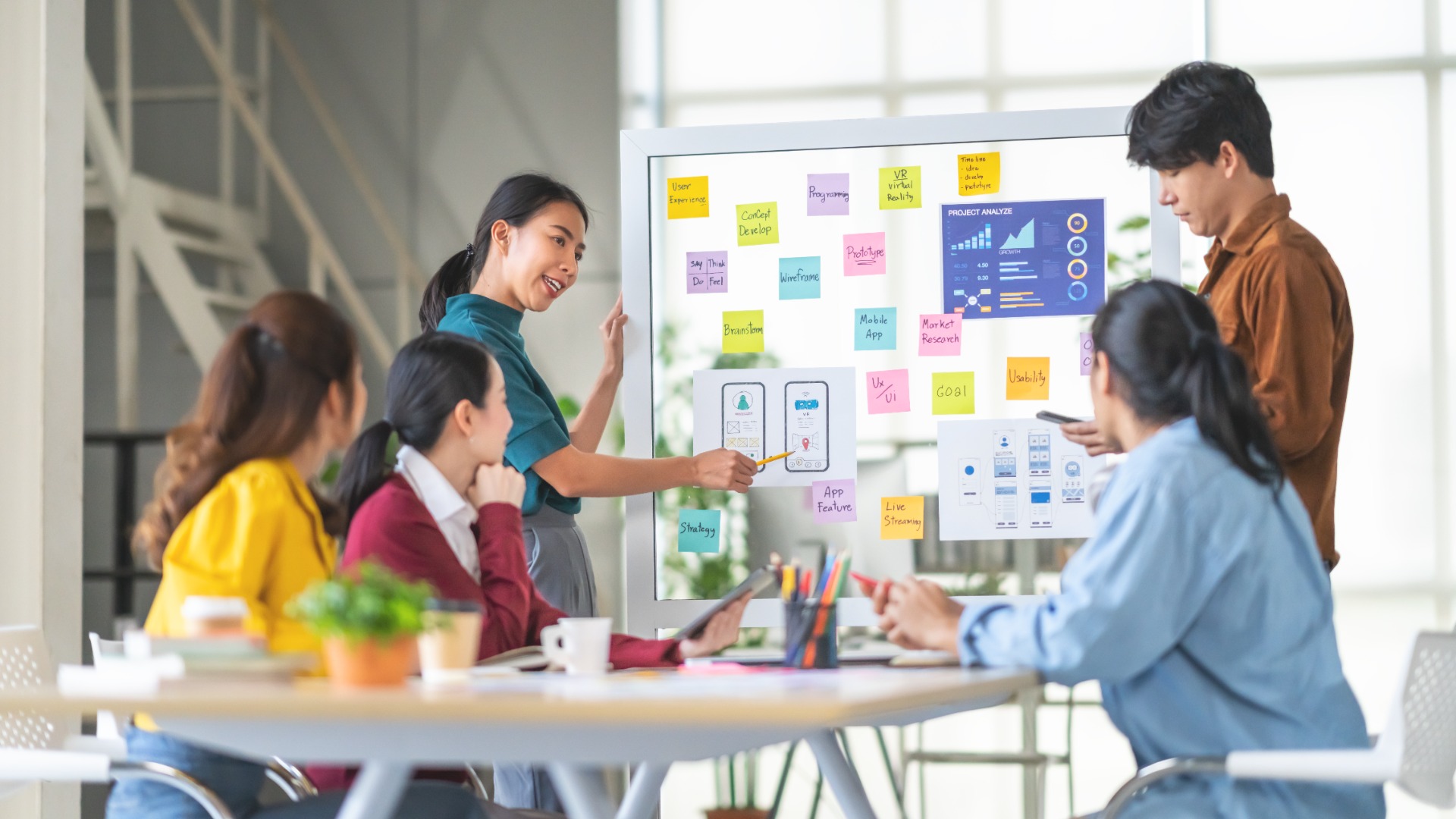
LEAN SOFTWARE DEVELOPMENT PRINCIPLES
Lean software development principles are derived from Lean manufacturing principles but tailored for software development processes. They aim to streamline workflows, improve efficiency, and deliver higher-quality software while minimizing waste. Here are some key Lean software development principles:
Eliminate Waste: Identify and eliminate waste in software development processes. This includes unnecessary features, overproduction, waiting time, rework, defects, and inefficient processes. Focus on delivering value to the customer while minimizing waste.
Amplify Learning: Encourage a culture of continuous learning and improvement. Embrace feedback from customers, stakeholders, and team members to refine requirements, adapt to changing needs, and optimize processes. Prioritize validated learning over speculation.
Decide as Late as Possible: Defer decisions until the last responsible moment to maximize flexibility and adaptability. Avoid making premature decisions based on incomplete or uncertain information. Delay commitments until the necessary information is available.
Deliver as Fast as Possible: Strive to deliver value to customers quickly and incrementally. Break down projects into small, manageable iterations or releases. Embrace iterative development, frequent deliveries, and continuous deployment to accelerate time-to-market.
Empower the Team: Empower cross-functional teams to make decisions and take ownership of their work. Encourage collaboration, autonomy, and self-organization. Trust teams to solve problems, innovate, and deliver results.
Build Integrity In: Focus on building quality into the software from the start. Prioritize code quality, automated testing, and continuous integration to detect defects early and ensure reliability. Emphasize simplicity, clarity, and maintainability in design and implementation.
Optimize the Whole: Optimize the entire software development process rather than individual parts. Align workflows, tools, and practices to maximize flow and minimize delays. Eliminate silos, handoffs, and bottlenecks that impede progress.
See the Whole: Take a holistic view of the software development process and its impact on the organization and stakeholders. Consider the end-to-end value stream, from ideation to delivery and beyond. Foster collaboration and transparency across teams and departments.
Respect People: Treat team members, customers, and stakeholders with respect and dignity. Value their expertise, perspectives, and contributions. Create a supportive and inclusive work environment that promotes trust, collaboration, and personal growth.
Optimize for Learning: Prioritize learning and experimentation over blame and punishment. Encourage risk-taking, innovation, and continuous improvement. Embrace failures as opportunities for learning and growth.
By embracing these Lean software development principles, teams can improve productivity, quality, and customer satisfaction while fostering a culture of continuous improvement and innovation.
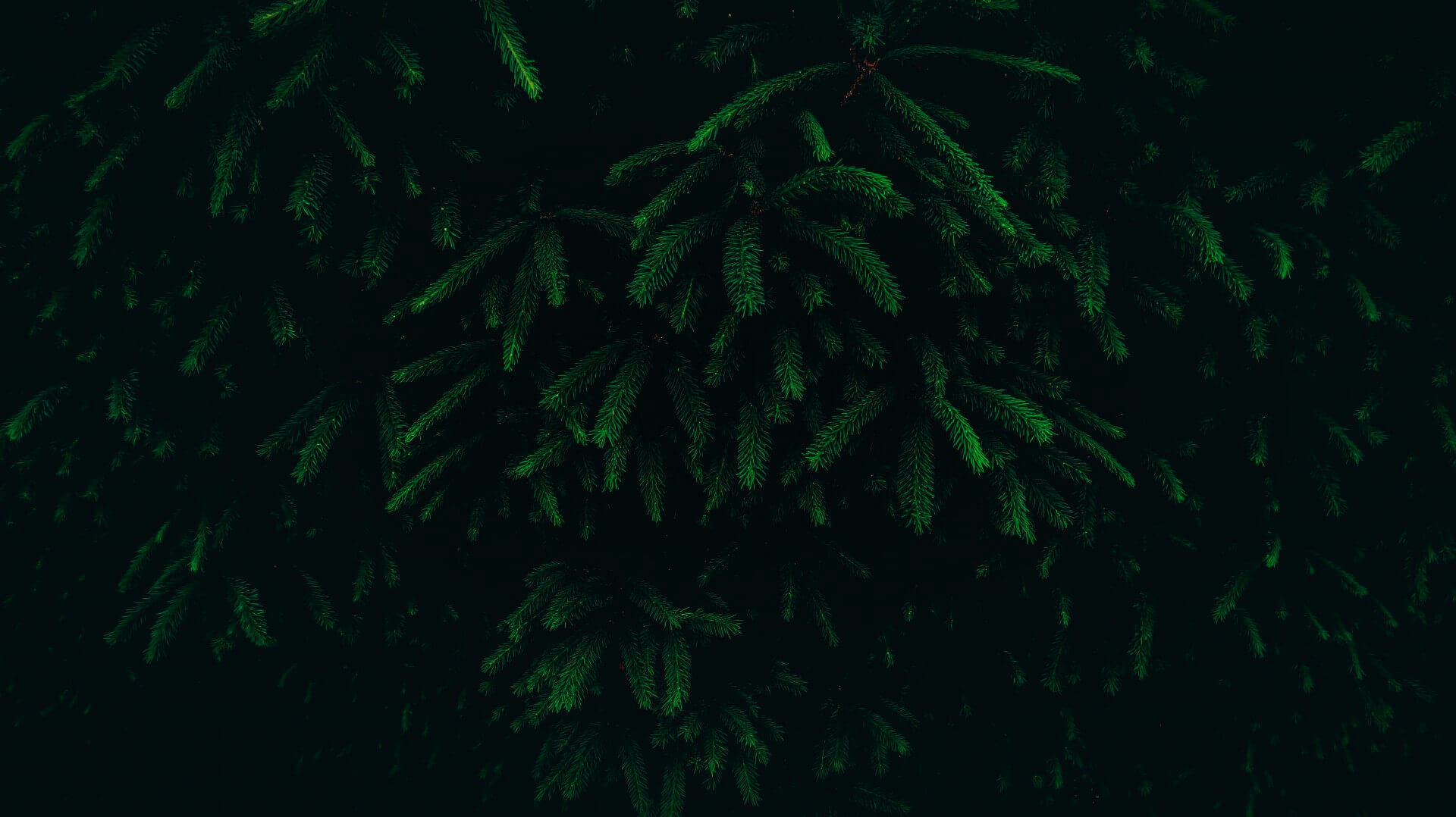
VALUE STREAM MAPPING
Value stream mapping (VSM) is a Lean management technique used to visualize and analyze the flow of materials and information required to bring a product or service from the beginning of the process (e.g., raw materials) to its delivery to the customer. It is a powerful tool for identifying waste, inefficiencies, and opportunities for improvement within a process. Here's an overview of value stream mapping in Lean:
Visual Representation: Value stream mapping involves creating a visual representation of the entire process, typically using a flowchart or diagram. The map illustrates each step in the process, including material flows, information flows, and process times.
Current State Mapping: The first step in value stream mapping is to map the current state of the process. This involves observing and documenting the flow of materials and information, including cycle times, lead times, inventory levels, and process steps. The goal is to gain a comprehensive understanding of how the process currently operates.
Identifying Value-Added and Non-Value-Added Activities: Value stream mapping distinguishes between value-added activities, which directly contribute to meeting customer requirements, and non-value-added activities, which do not. By analyzing each process step, teams can identify and eliminate waste, such as overproduction, waiting, unnecessary transportation, and rework.
Future State Mapping: Once the current state is understood and waste is identified, teams can develop a future state map that represents an ideal, optimized version of the process. This involves redesigning the process to eliminate waste, improve flow, and increase efficiency. Future state mapping may involve implementing Lean tools and techniques, reorganizing work areas, or redesigning workflows.
Implementation Plan: After creating the future state map, teams develop an implementation plan to achieve the desired improvements. This may involve implementing changes gradually, monitoring performance metrics, and continuously refining the process based on feedback and results.
Continuous Improvement: Value stream mapping is a continuous improvement tool, meaning that the process of analyzing and optimizing the value stream is ongoing. Teams regularly review and update their value stream maps to ensure that they remain aligned with business goals, customer requirements, and changing market conditions.
Overall, value stream mapping is a fundamental Lean tool for identifying opportunities for improvement, reducing waste, and optimizing processes to deliver greater value to customers.
Process Cycle Efficiency (PCE):
- Process Cycle Efficiency measures the efficiency of a process by determining the ratio of value-added time to total cycle time.
- It represents the percentage of time within a process that is spent on activities that directly add value to the product or service, as opposed to non-value-adding activities.
- The formula for calculating PCE is: PCE = (Value-added time / Total cycle time) * 100%
- A higher PCE indicates a more efficient process with minimal waste and a higher proportion of value-adding activities.
- PCE is a useful metric for identifying opportunities to eliminate waste, reduce cycle times, and improve overall process performance.
In summary, Value Stream Mapping is a visual tool used to analyze and optimize the entire value stream, while Process Cycle Efficiency is a metric used to measure the efficiency of individual processes within the value stream. Both tools are valuable for identifying opportunities for improvement and driving continuous improvement initiatives in Lean manufacturing and process improvement efforts.
Sample Questions on Lean (MCQs)
1. What is the primary objective of Lean methodology?
A) Increasing production speed
B) Eliminating waste and maximizing value
C) Reducing employee workload
D) Delivering products with minimal effort
✅ B) Eliminating waste and maximizing value
Explanation: Lean focuses on eliminating waste (Muda) while ensuring that every process step adds value to the customer.
2. Which of the following is NOT considered a type of waste (Muda) in Lean?
A) Overproduction
B) Excessive inventory
C) Continuous improvement
D) Unnecessary motion
✅ C) Continuous improvement
Explanation: Continuous improvement (Kaizen) is a core Lean principle, not waste. Waste includes overproduction, waiting, and excessive inventory.
3. What is the main goal of Value Stream Mapping (VSM)?
A) To increase profits
B) To visualize and identify waste in a process
C) To measure employee performance
D) To track budget expenses
✅ B) To visualize and identify waste in a process
Explanation: VSM is used to map out the flow of materials and information to identify waste and opportunities for process improvement.
4. The Lean principle "Just-in-Time" (JIT) aims to:
A) Deliver work as soon as possible
B) Reduce inventory and produce only what is needed
C) Hire new employees only when required
D) Decrease customer involvement
✅ B) Reduce inventory and produce only what is needed
Explanation: JIT ensures that resources are used efficiently by producing only what is required, reducing excess inventory.
5. What does "Kaizen" mean in Lean?
A) Rapid restructuring of a business
B) Continuous improvement
C) Employee replacement strategy
D) Fixed production planning
✅ B) Continuous improvement
Explanation: Kaizen focuses on small, incremental improvements over time to enhance efficiency and quality.
6. Which of the following is a key Lean tool used for problem-solving?
A) Pareto Chart
B) Gantt Chart
C) Fishbone Diagram
D) Scrum Board
✅ C) Fishbone Diagram
Explanation: The Fishbone Diagram (Ishikawa) helps identify root causes of problems by categorizing potential factors.
7. What is the "pull system" in Lean?
A) Work is assigned based on strict deadlines
B) Work is started only when there is demand
C) Managers assign work without employee input
D) Employees select tasks randomly
✅ B) Work is started only when there is demand
Explanation: The pull system ensures work begins only when there is actual demand, reducing waste and overproduction.
8. What does the term "Heijunka" mean in Lean?
A) Employee rotation
B) Production leveling
C) Waste reduction
D) Supplier collaboration
✅ B) Production leveling
Explanation: Heijunka ensures a stable and consistent workflow by leveling production, reducing overburden and uneven workloads.
9. Which Lean tool is used for workplace organization?
A) 5S
B) VSM
C) PDCA
D) Agile
✅ A) 5S
Explanation: 5S (Sort, Set in order, Shine, Standardize, Sustain) organizes workspaces to improve efficiency and safety.
10. What is the primary goal of the Lean "Gemba Walk"?
A) To observe processes in the actual work environment
B) To conduct virtual meetings
C) To increase marketing outreach
D) To implement strict employee rules
✅ A) To observe processes in the actual work environment
Explanation: The Gemba Walk involves managers going to the workplace to understand workflows, identify waste, and promote improvements.
11. What is the main benefit of using PDCA (Plan-Do-Check-Act)?
A) It speeds up decision-making
B) It ensures continuous process improvement
C) It reduces employee workload
D) It standardizes all workflows
✅ B) It ensures continuous process improvement
Explanation: PDCA is a cycle that helps organizations improve processes through iterative planning, execution, evaluation, and refinement.
12. Which of the following is NOT a Lean principle?
A) Define value
B) Create flow
C) Implement strict deadlines
D) Establish pull
✅ C) Implement strict deadlines
Explanation: Lean focuses on flexibility, reducing waste, and optimizing flow rather than imposing rigid deadlines.
13. What does "Mura" refer to in Lean?
A) Unevenness in production
B) Excessive inventory
C) Unnecessary motion
D) Employee turnover
✅ A) Unevenness in production
Explanation: Mura refers to inconsistencies in workload distribution, leading to inefficiencies and bottlenecks.
14. Which Lean tool helps in identifying non-value-adding activities?
A) 5 Whys
B) Kanban Board
C) Value Stream Mapping
D) Daily Stand-ups
✅ C) Value Stream Mapping
Explanation: VSM helps identify waste and inefficiencies in the workflow by mapping each process step.
15. The primary focus of Lean is on:
A) Customer value
B) Employee training
C) Reducing IT costs
D) Long meetings
✅ A) Customer value
Explanation: Lean prioritizes delivering value to customers by eliminating waste and improving processes.
16. Which Lean tool is used to identify the root cause of a problem?
A) Pareto Chart
B) 5 Whys
C) Sprint Retrospective
D) Risk Register
✅ B) 5 Whys
Explanation: The 5 Whys technique repeatedly asks "Why?" to trace a problem back to its root cause.
17. What is "Muri" in Lean?
A) Overburdening employees or equipment
B) A cost-cutting strategy
C) A method to increase defects
D) A performance review metric
✅ A) Overburdening employees or equipment
Explanation: Muri refers to excessive strain on resources, leading to inefficiency and errors.