KANBAN
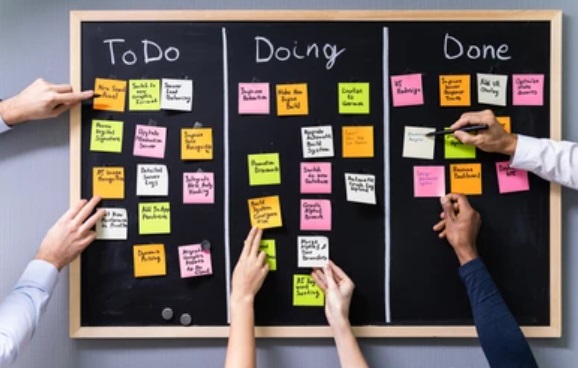
Kanban is a popular Agile framework used for managing work on a visual board. It originated from Toyota's manufacturing process and has since been adapted for various industries, including software development, project management, and other knowledge work domains.
Here's a brief overview of how Kanban works:
Visual Board: At the heart of Kanban is a visual board divided into columns representing different stages of the workflow. Typically, these columns include states like "To Do," "In Progress," and "Done," but they can be customized based on the specific needs of the team or project.
Work Items: Work items, often represented by cards or sticky notes, move through the columns on the board as they progress from initiation to completion.
Work in Progress (WIP) Limits: Kanban emphasizes limiting the amount of work in progress at any given time to avoid overburdening the team and maintain a steady flow of work. WIP limits are set for each column to ensure that teams focus on completing tasks before starting new ones.
Continuous Improvement: Kanban encourages continuous improvement through the use of metrics and regular retrospectives. Teams monitor key performance indicators (KPIs) such as lead time and cycle time to identify bottlenecks and areas for improvement.
Pull System: Kanban operates on a pull-based system, meaning that work is pulled into the system only when there is capacity to handle it, rather than being pushed onto the team. This helps prevent overloading and ensures that the team can maintain a sustainable pace.
Adaptability: Kanban is highly adaptable and can be used in conjunction with other Agile methodologies such as Scrum or Lean. Teams can tailor the framework to suit their specific needs and processes.
Overall, Kanban promotes transparency, collaboration, and efficiency by visualizing work, limiting work in progress, and fostering a culture of continuous improvement. It's a flexible framework that can be applied to a wide range of projects and teams.
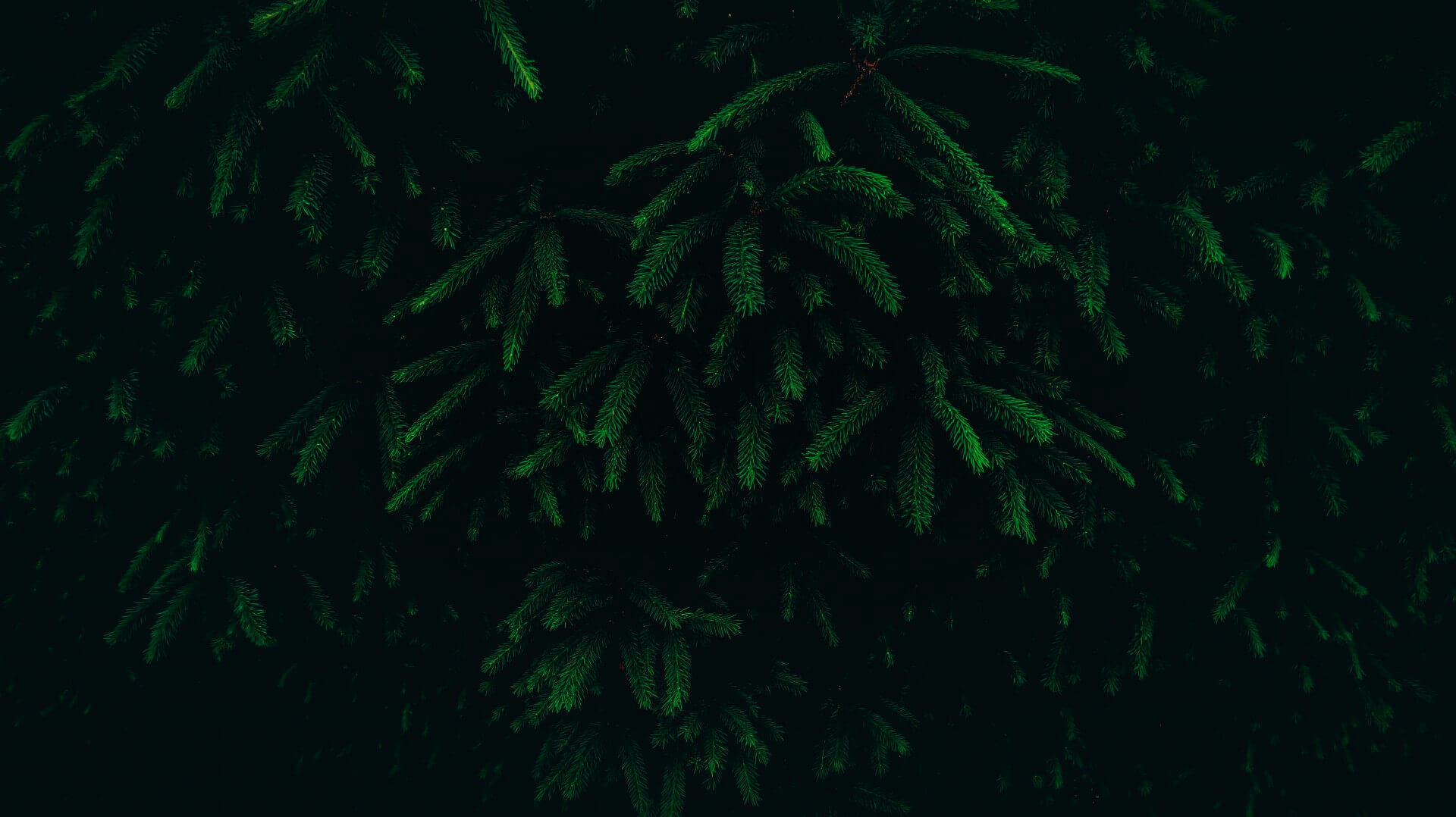
KANBAN METRICS
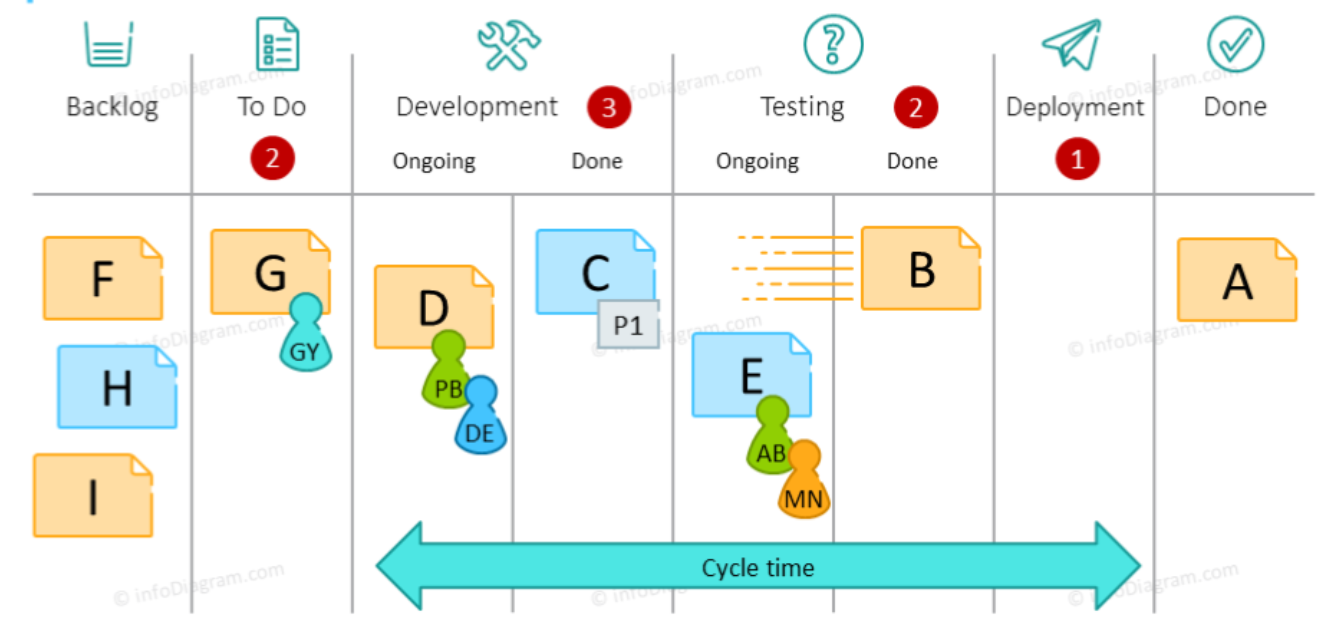
Kanban is a popular method used in software development and project management to visualize and manage work. While there are various metrics used in Kanban to measure performance and improve processes, here are some common ones:
Lead Time: The time it takes for a task or work item to move from the starting point to completion. This metric helps in understanding the efficiency of the workflow and identifying bottlenecks.
Cycle Time: Similar to lead time, cycle time measures the time it takes for a task to be completed once work begins on it. It excludes waiting time and focuses solely on the time spent actively working on the task.
Throughput: The number of tasks or work items completed within a specific time period. Throughput helps in assessing the team's productivity and capacity.
Work In Progress (WIP): The number of tasks or work items that are currently in progress but not yet completed. Monitoring WIP helps in maintaining a manageable workload and identifying potential overburdening.
Cumulative Flow Diagram (CFD): A graphical representation showing the flow of work items through different stages of the workflow over time. CFDs help in visualizing bottlenecks, tracking progress, and predicting future trends.
Blocked Time: The amount of time a task spends waiting for external dependencies or unresolved issues. Monitoring blocked time helps in identifying impediments and improving workflow efficiency.
Aging Work Items: The duration for which tasks or work items have been in the system without making progress. Aging work items highlight areas of stagnation and help in prioritizing tasks.
Escaped Defects: The number of defects or issues identified after a task or work item has been completed and delivered to the customer. Tracking escaped defects helps in improving quality and identifying areas for improvement in the development process.
SLE forecasts: How long it should take a given item to flow from start to finish within your workflow. The SLE itself has two parts: a period of elapsed days and a probability associated with that period (e.g., "75% of work items will be finished in 7 days or less" which can also be stated as "7 days with 75% confidence/probability").
These metrics provide valuable insights into the performance of Kanban systems and help teams identify areas for improvement to enhance efficiency, productivity, and quality.
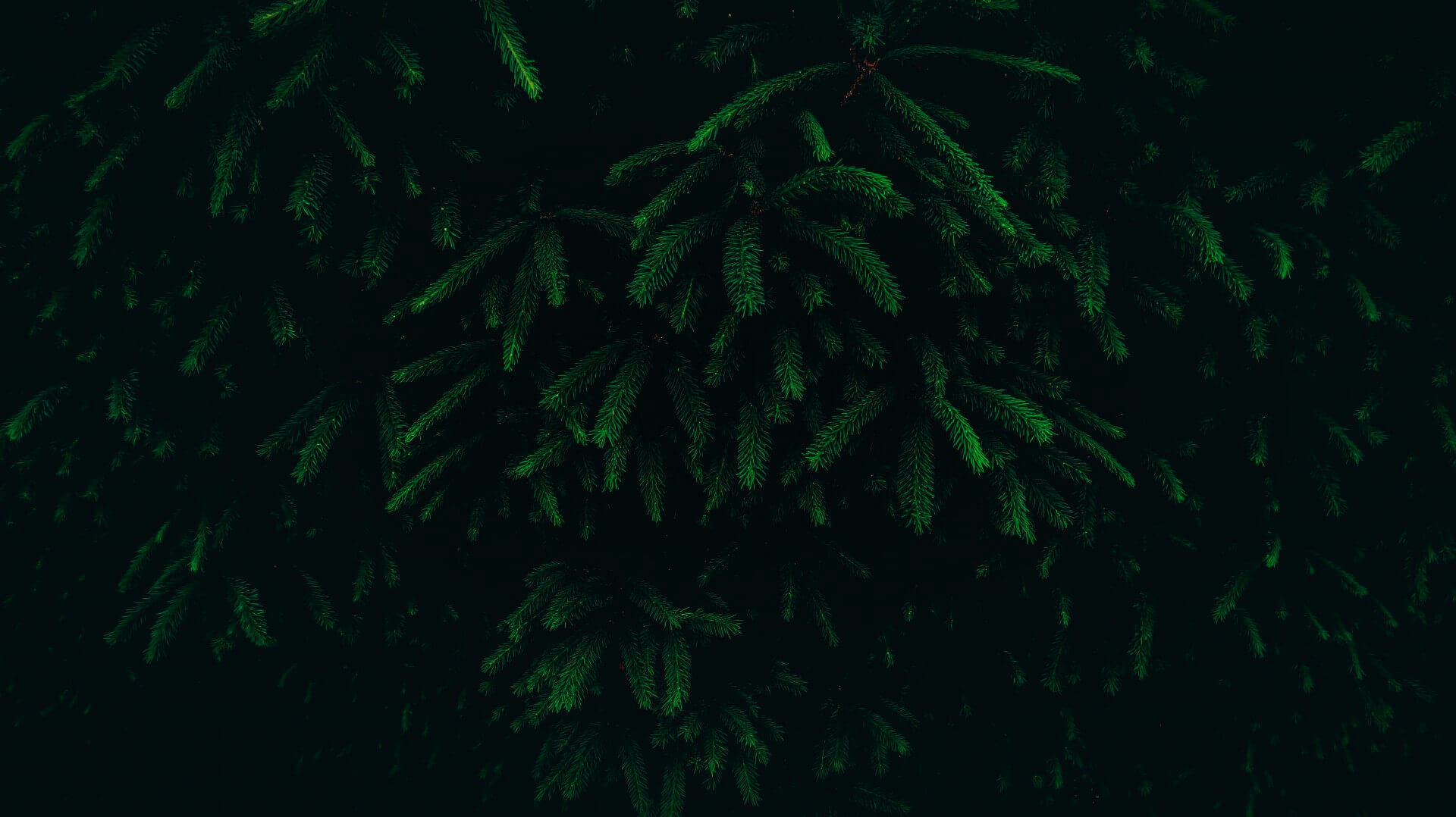
Little's law
Little's Law is a fundamental concept in queuing theory that is often applied in the context of Kanban systems. Little's Law states that the average number of items in a system (L) is equal to the average arrival rate of items (λ) multiplied by the average time each item spends in the system (W). Mathematically, it can be expressed as:
L= λ×W OR Throughput = WIP/Cycle Time
In the context of Kanban, Little's Law helps teams understand and optimize their workflow by providing insights into key performance metrics. Here's how it relates to Kanban:
Average Number of Items in the System (L): In a Kanban system, this refers to the average number of work items (such as user stories, tasks, or features) that are in progress or in the queue at any given time. Understanding this metric helps teams identify bottlenecks and manage their work in progress (WIP) limits effectively.
Average Arrival Rate of Items (λ): This represents the rate at which new work items are entering the system. It could be the number of new user stories being added to the backlog per day or any other relevant time period. By monitoring this metric, teams can gauge the demand on their system and adjust their capacity accordingly.
Average Time Each Item Spends in the System (W): Also known as cycle time, this metric measures the average time it takes for a work item to move through the entire workflow from start to finish. By analyzing cycle time, teams can identify inefficiencies, streamline their processes, and improve overall productivity.
By applying Little's Law in the context of Kanban, teams can gain valuable insights into their workflow dynamics and make data-driven decisions to optimize their processes, improve throughput, and deliver value more efficiently.
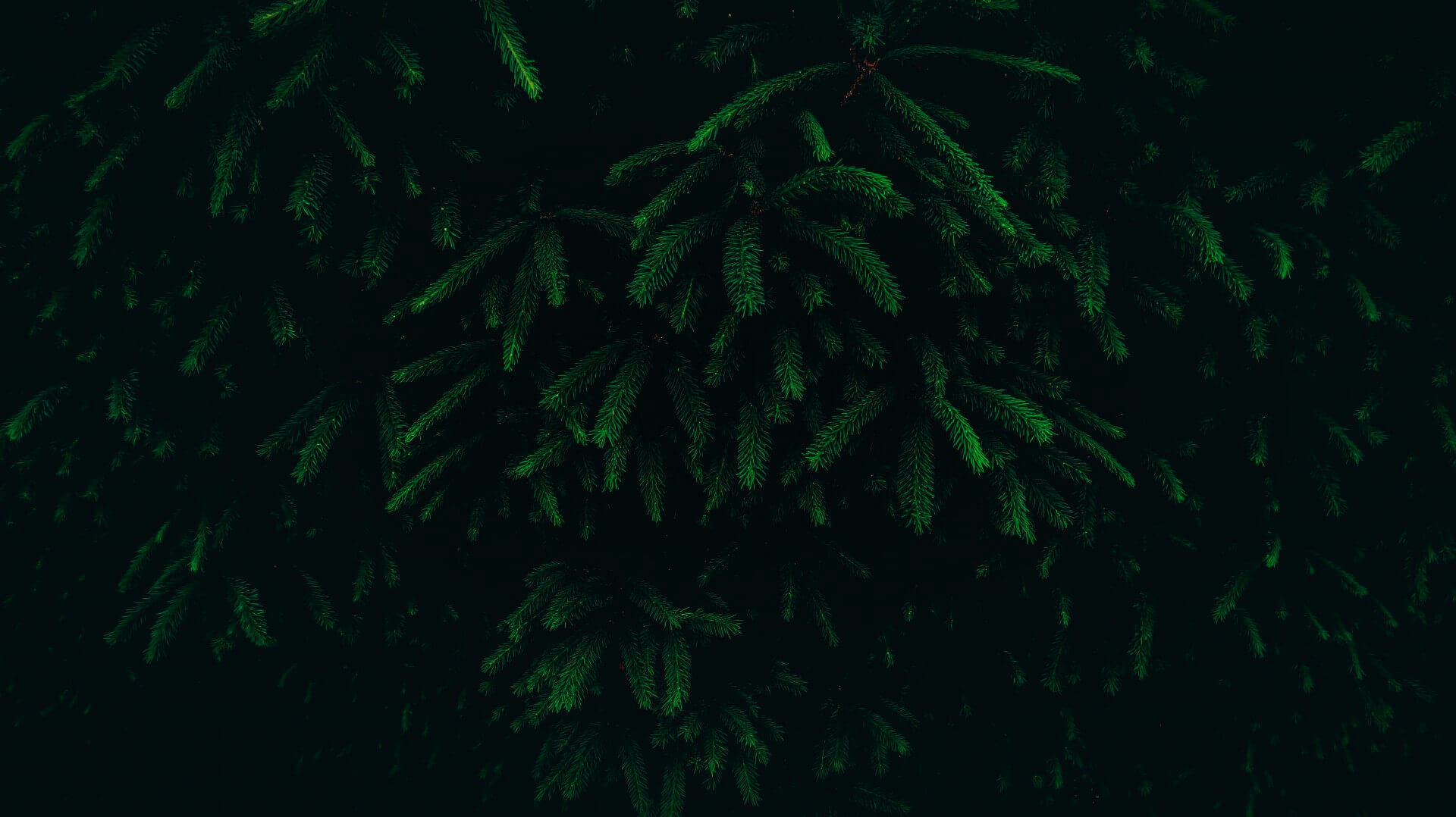
KANBAN PRINCIPLES
Kanban is a popular agile framework for managing work in a visual manner. It is based on several key principles:
Visualize Workflow: The fundamental concept of Kanban is to visualize the workflow. This means representing each work item (task, user story, etc.) as a card on a Kanban board, where columns represent different stages of the workflow (e.g., "To Do," "In Progress," "Done").
Limit Work in Progress (WIP): Kanban emphasizes limiting the amount of work that is actively being worked on at any given time. By setting WIP limits for each stage of the workflow, teams can avoid overloading themselves, reduce multitasking, and maintain a steady flow of work.
Manage Flow: The goal of Kanban is to achieve a smooth, continuous flow of work through the system, from start to finish. Teams focus on optimizing flow by identifying and addressing bottlenecks, reducing cycle times, and improving efficiency.
Make Policies Explicit: Kanban encourages teams to define explicit policies for how work moves through the workflow. These policies clarify expectations, establish standards, and provide guidance for team members, ensuring consistent and transparent decision-making.
Implement Feedback Loops: Feedback loops are essential for continuous improvement in Kanban. Teams regularly review performance metrics, such as lead time and cycle time, and use this data to identify opportunities for improvement, adjust their processes, and make informed decisions.
Improve Collaboratively, Evolve Experimentally: Kanban promotes a culture of collaboration and experimentation. Teams continuously seek opportunities to improve their processes, experiment with new approaches, and adapt to changing circumstances through incremental changes.
Encourage Leadership at All Levels: In Kanban, leadership is distributed across the team, and everyone is encouraged to take ownership of their work and contribute to the improvement of the system. This decentralized approach fosters autonomy, accountability, and innovation.
By adhering to these principles, teams can leverage Kanban to optimize their workflow, increase productivity, and deliver value more effectively.
Sample Questions(MCQs) on KANBAN
Kanban MCQs
1. What is the primary purpose of Kanban?
A) To assign tasks randomly
B) To visually manage workflow and optimize efficiency
C) To increase the number of employees
D) To eliminate the need for planning
✅ B) To visually manage workflow and optimize efficiency
Explanation: Kanban is a visual system that helps teams track work in progress and optimize flow by reducing bottlenecks.
2. What does a Kanban board primarily consist of?
A) Task lists and reports
B) Columns representing workflow stages and work items
C) Employee performance charts
D) Budget tracking sheets
✅ B) Columns representing workflow stages and work items
Explanation: A Kanban board visually represents workflow with columns (e.g., "To Do," "In Progress," "Done"), helping teams track progress.
3. What does WIP stand for in Kanban?
A) Work in Planning
B) Work in Progress
C) Weekly Inventory Process
D) Waste in Production
✅ B) Work in Progress
Explanation: WIP (Work in Progress) represents tasks actively being worked on and is a key concept in managing flow efficiency.
4. What is the purpose of WIP limits in Kanban?
A) To assign more tasks to employees
B) To limit the number of tasks in each workflow stage
C) To eliminate tasks from the backlog
D) To measure employee efficiency
✅ B) To limit the number of tasks in each workflow stage
Explanation: WIP limits prevent bottlenecks by capping the number of ongoing tasks, ensuring smooth workflow.
5. What kind of work is best suited for Kanban?
A) Repetitive, continuous workflow processes
B) Strictly deadline-driven projects
C) One-time projects with fixed phases
D) Non-structured brainstorming sessions
✅ A) Repetitive, continuous workflow processes
Explanation: Kanban is ideal for managing continuous and workflow-driven tasks such as software development and IT support.
6. Which principle does Kanban follow?
A) Push system
B) Pull system
C) Fixed scheduling system
D) Hierarchical approval system
✅ B) Pull system
Explanation: In a pull system, work is started only when there is capacity, preventing overloading and improving flow.
7. What does "Lead Time" measure in Kanban?
A) The time from task initiation to completion
B) The time taken to complete a sprint
C) The hours an employee spends on a task
D) The estimated time to deliver a product
✅ A) The time from task initiation to completion
Explanation: Lead Time measures the total duration a task takes from request to completion, helping track efficiency.
8. What is "Cycle Time" in Kanban?
A) The time taken to complete a task after work begins
B) The total project duration
C) The number of employees working on a project
D) The number of completed tasks in a week
✅ A) The time taken to complete a task after work begins
Explanation: Cycle Time tracks how long a task remains in the "In Progress" stage, helping teams analyze efficiency.
9. What is the primary function of a "Done" column in Kanban?
A) To track pending approvals
B) To store completed tasks
C) To assign new tasks
D) To list backlog items
✅ B) To store completed tasks
Explanation: The "Done" column represents work that has been completed and delivered.
10. What is "Kaizen" in Kanban?
A) A daily stand-up meeting
B) A principle of continuous improvement
C) A type of Kanban board
D) A defect management process
✅ B) A principle of continuous improvement
Explanation: Kaizen focuses on making small, continuous improvements to enhance workflow efficiency.
11. What is a "Swimlane" in Kanban?
A) A task tracking tool
B) A horizontal division on a Kanban board to separate work categories
C) A metric for tracking employee performance
D) A backlog prioritization method
✅ B) A horizontal division on a Kanban board to separate work categories
Explanation: Swimlanes help organize tasks by priority, team, or type of work.
12. What is the first step in implementing Kanban?
A) Assigning WIP limits
B) Visualizing the workflow
C) Hiring a Kanban consultant
D) Automating all processes
✅ B) Visualizing the workflow
Explanation: Kanban starts by mapping the existing workflow on a visual board to identify inefficiencies.
13. What does "Throughput" measure in Kanban?
A) The number of completed tasks in a given time
B) The number of ongoing tasks
C) The number of backlog items
D) The speed of individual task completion
✅ A) The number of completed tasks in a given time
Explanation: Throughput measures how many work items are completed in a specific timeframe.
14. Kanban follows which type of improvement process?
A) Iterative and incremental
B) Waterfall methodology
C) Fixed scope and rigid planning
D) Top-down management changes
✅ A) Iterative and incremental
Explanation: Kanban allows for continuous, incremental improvements rather than rigid planning.
15. How often should a Kanban board be updated?
A) Monthly
B) Weekly
C) Daily or in real-time
D) Only at the end of a project
✅ C) Daily or in real-time
Explanation: Kanban boards should be updated continuously to reflect real-time workflow progress.
16. What happens when a task reaches a WIP limit in Kanban?
A) Work is paused until tasks are completed
B) New tasks are added without restriction
C) Tasks are reassigned to other team members
D) Work on all projects is stopped
✅ A) Work is paused until tasks are completed
Explanation: WIP limits prevent overloading by ensuring that no new tasks are started until current tasks are completed.
17. What is the primary difference between Kanban and Scrum?
A) Kanban is iterative, while Scrum is continuous
B) Scrum uses fixed sprints, while Kanban is flow-based
C) Kanban requires a dedicated Scrum Master
D) Scrum does not allow visual tracking
✅ B) Scrum uses fixed sprints, while Kanban is flow-based
Explanation: Kanban is a continuous workflow system, while Scrum follows time-boxed iterations (sprints).
18. Which industry originally developed Kanban?
A) Software development
B) Construction
C) Manufacturing (Toyota)
D) Marketing
✅ C) Manufacturing (Toyota)
Explanation: Toyota developed Kanban in the 1940s as a way to optimize production efficiency.
19. What happens when a bottleneck occurs in Kanban?
A) Additional WIP limits are added
B) Work stops completely
C) The team focuses on resolving the bottleneck before adding new work
D) Tasks are moved to the backlog
✅ C) The team focuses on resolving the bottleneck before adding new work
Explanation: Kanban helps teams identify and address bottlenecks to maintain workflow efficiency.
20. What is the best way to improve efficiency in a Kanban system?
A) Increasing WIP limits
B) Ignoring workflow bottlenecks
C) Continuously monitoring and optimizing processes
D) Assigning all tasks to one team member
✅ C) Continuously monitoring and optimizing processes
Explanation: Continuous monitoring and improvement (Kaizen) ensure that workflows remain efficient and adaptable.